The hot-dip galvanizing production line serves as the backbone of the steel industry, providing essential corrosion protection. Cobalt alloy has become an indispensable asset in these harsh environments, offering unparalleled advantages. Let’s explore how cobalt alloy products fundamentally transform the hot-dip galvanizing process.
Why is Cobalt Alloy Suitable for Hot-Dip Galvanizing Production Lines?
In hot-dip galvanizing production lines, the challenges posed by extreme operating conditions are manifold—high temperatures, essential for melting zinc, subject equipment to prolonged exposure, and accelerating wear and deformation. The demand for high capacity often pushes production lines to operate at high speeds, increasing stress and the risk of premature failure. Furthermore, prolonged contact with corrosive molten zinc hastens equipment corrosion, reducing lifespan.
Cobalt alloy is a good solution for addressing these challenges. Renowned for its exceptional resistance to wear, high temperatures, and corrosion, Cobalt alloy can significantly enhance the durability and performance of equipment in hot-dip galvanizing production lines. By integrating Cobalt alloy components, operators can mitigate the adverse effects of high temperatures, extend equipment lifespan, and ensure operational efficiency even in the most demanding environments.
How to Choose Cobalt Alloys in Hot-Dip Galvanizing Production Lines?
In hot-dip galvanizing production, cobalt alloys reign supreme, serving as the cornerstone for essential components. These alloys find their place in crafting sinking roller bushings, stabilizing roller bushings, bearing bushes, caps, scrapers, and more, ensuring seamless operation across diverse production line conditions.
Galvanizing production lines, each with its unique temperature and speed specifications, demand tailored solutions. For high-temperature, high-speed lines operating between 650-720 degrees Celsius, T800 material bushings prove indispensable, boasting a service life of 4 to 5 days. Conversely, low-temperature, high-speed lines, ranging from 490-520 degrees Celsius, opt for Co 4 bushings, delivering an impressive service life of 20-25 days. Meanwhile, Co 6 bushings are the most cost-effective option for low-temperature, low-speed lines.
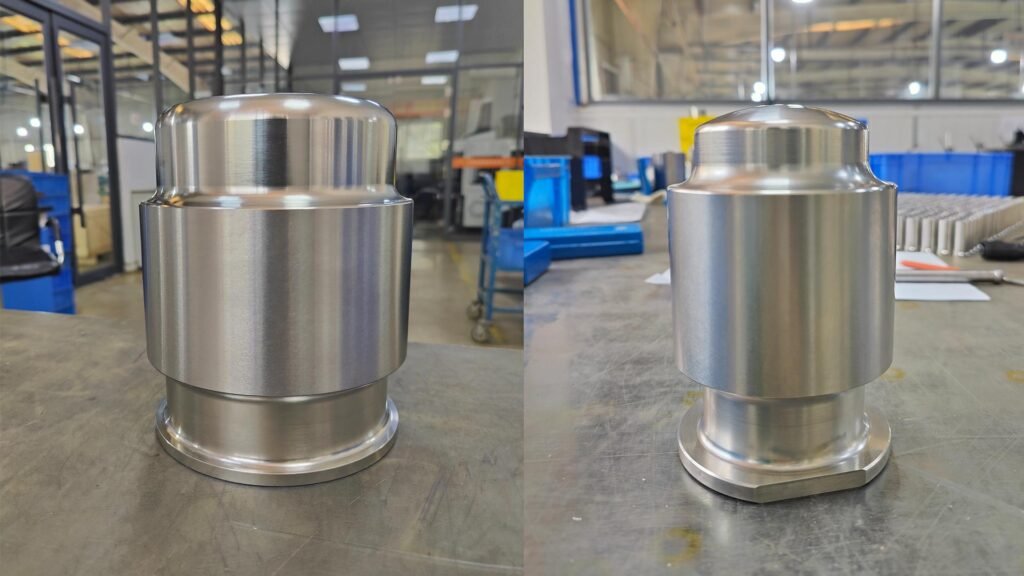
The choice of bearing bush depends on meticulous consideration of material and hardness. Combining different hardnesses, typically utilizing Co 6, T800, or ceramic materials, ensures prolonged service life and optimal performance.
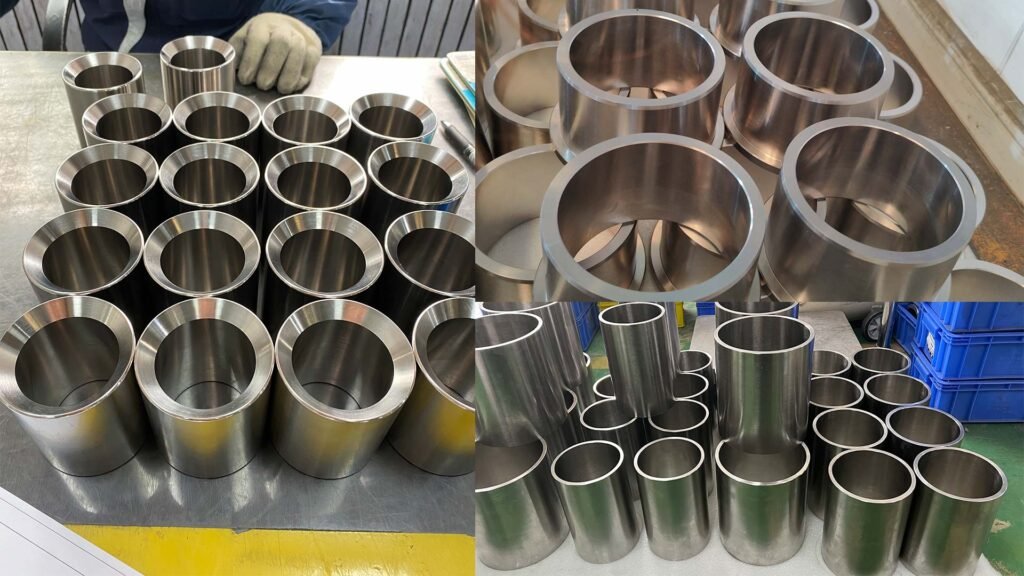
End Caps are crafted from the same material as the bushings to uphold integrity throughout the system.

Scraper components play a crucial role in maintaining the purity of the zinc bath, where Co 6 is usually the material of choice, standing resilient against harsh conditions while safeguarding production integrity.
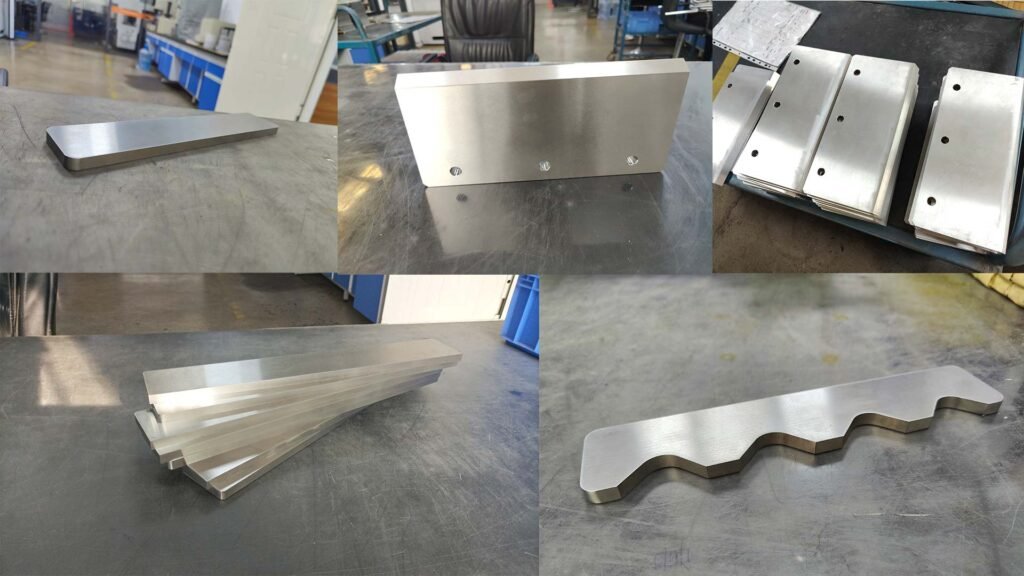
With Cobalt alloys at the helm, hot-dip galvanizing production lines optimize efficiency, durability, and performance, ensuring operation across varied environments and demands.
SYTOP Your Trusted Partner for Cobalt Alloy Solutions
SYTOP is a leading manufacturer of cobalt alloys in China. It has extensive expertise and a proven track record in the hot-dip galvanizing sector. With years of dedicated focus on this industry, SYTOP has cultivated many production experiences, delivering high-quality cobalt alloy solutions tailored to the unique demands of hot-dip galvanizing applications. From sinking roller bushings to stabilizing roller bushings, bearing bushes, plugs, scrapers, and beyond, SYTOP’s comprehensive range of cobalt alloy products ensures optimal performance and durability across diverse production line conditions. Trust SYTOP as your partner and experience the reliability, efficiency, and longevity that only top-tier cobalt alloy solutions can provide in the hot-dip galvanizing industry.